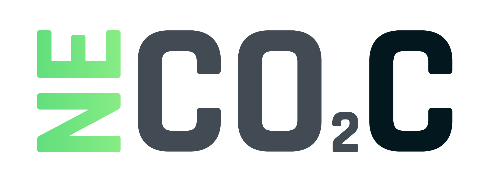
Verbundvorhaben NECOC – Schaffung negativer Emissionen durch Auftrennung von atmosphärischem CO2 in wirtschaftlich verwertbaren Kohlenstoff und Sauerstoff
- Ansprechperson:
- Förderung:
Bundesministerium für Wirtschaft und Energie
- Projektbeteiligte:
- Meldung der Gips-Schüle-Stiftung im Oktober 2023
- Beitrag beim BMWK-Fachportal vom 25.10.2023
- Bericht in den KIT News vom 25.10.2023
- Videobeitrag der FAZ vom 08.02.2023
- Beitrag bei NTV vom 07.02.2023
- Meldung auf der Homepage des Landtags Ba-Wü vom 05.02.2023
- Beitrag beim Deutschlandfunk vom 16.01.2023
- Pressemitteilung KIT vom 06.12.2022
- Pressemitteilung BMWK vom 06.12.2022
- Interview zur Pressemitteilung BMWK vom 06.12.2022
- Energie von morgen vom 11.04.2022
- Pressemitteilung KIT vom 07.04.2022
- lookKIT 2022/01: Nachhaltig digital
- Wissenschaftsplattform Klimaschutz Jahresgutachten 2021
- Bundesbericht Energieforschung 2021
- Beitrag in der PROCESS vom 18.05.2020
- Beitrag in der BNN vom 05.05.2020
- Pressemitteilung KIT vom 25.03.2020
Publikationen
Gips-Schüle-Forschungspreis 2023 für NECOC
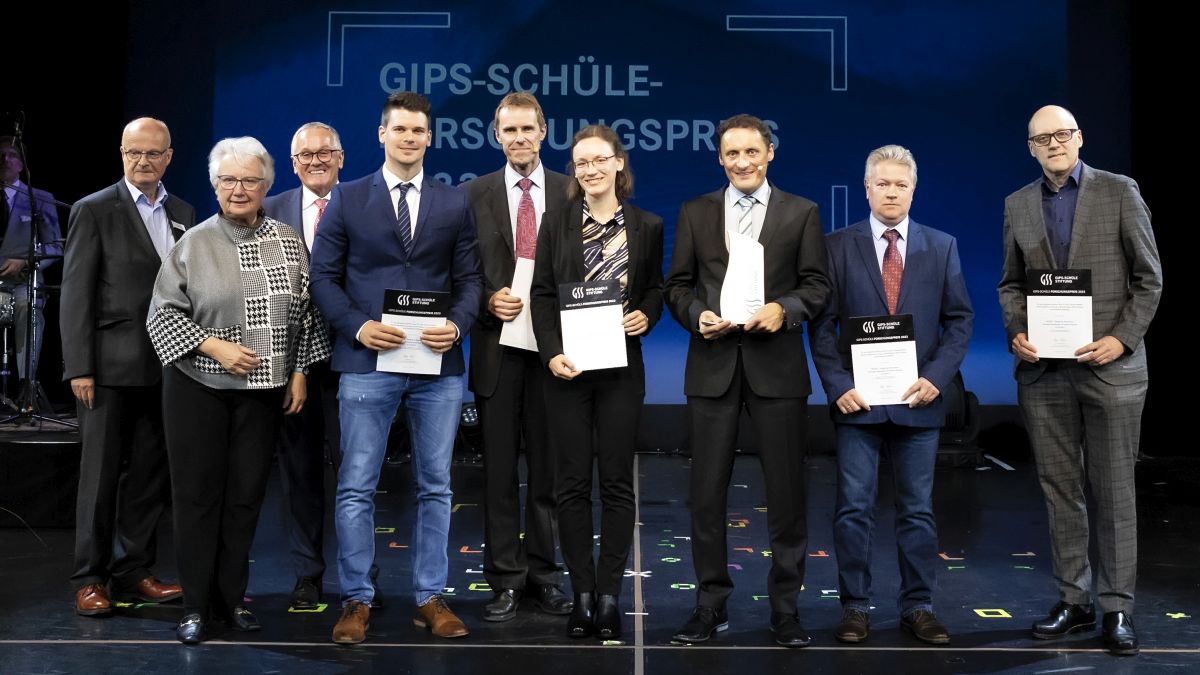
Film der Gips-Schüle-Stiftung über die Preisträger
Fester Kohlenstoff wird als industrieller Rohstoff etwa bei der Produktion von Batterien, in der Farbindustrie oder auch bei der Herstellung von Baustoffen eingesetzt. Bislang stammt er meist aus fossilen Quellen und wird unter Freisetzung enormer CO2-Emissionen produziert. Mit dem NECOC-Verfahren (Negative Emissions through converting Carbon diOxide to Carbon) entwickeln Forschende des Karlsruher Instituts für Technologie (KIT) mit Industriepartnern einen klimafreundlichen Produktionsweg, bei dem durch die Entnahme des CO2 aus der Umgebungsluft gleichzeitig sogenannte Negative Emissionen ermöglicht werden. Die Stuttgarter Gips-Schüle-Stiftung würdigte dieses Vorhaben nun mit dem renommierten Gips-Schüle-Forschungspreis. Die Preisverleihung fand am 24. Oktober 2023 in Stuttgart statt.
Link zur kompletten KIT-Presseinformation
Presseinformation der Gips-Schüle-Stiftung
Projektbeschreibung
Mit dem Pariser Klimaabkommen von 2015 hat sich die Weltgemeinschaft verpflichtet, die globale Erderwärmung bis zum Ende des Jahrhunderts auf unter zwei Grad Celsius zu begrenzen. Um dieses Ziel noch zu erreichen, sind neben den globalen Anstrengungen zur Reduktion der Treibhausgasemissionen auch Lösungen erforderlich, um bereits emittiertes CO2 wieder aus der Atmosphäre zu entfernen. Übergeordnetes Ziel dieses Vorhabens ist die Realisierung eines neuartigen Prozesses zur Schaffung „negativer Emissionen“, wobei atmosphärisches Kohlendioxid in elementaren, sehr reinen Kohlenstoff (Carbon Black) und Sauerstoff zerlegt wird. Dazu wird eine Demonstrationsanlage konzipiert, gebaut und über einen längeren Zeitraum betrieben. Im geplanten Prozess (vgl. Abb. 1) wird Umgebungsluft angesaugt und CO2 durch Adsorption herausgefiltert. Dieses wird mit Wasserstoff in einem mikrostrukturierten Reaktor zu Methan und Wasser umgesetzt. In weiteren Prozessschritten wird das CH4 in einem Flüssigmetall-Blasensäulenreaktor pyrolysiert, d.h. in H2 und C zerlegt, und das H2O durch mit Sonnenenergie betriebener Elektrolyse in O2 und H2 aufgespalten, wobei diese jedoch im Rahmen von NECOC nicht realisiert wird. Der Kohlenstoff fällt in Form von mikrogranularem Pulver an und kann wirtschaftlich z.B. in der Bau-, Gummi-, oder Elektronikindustrie verwertet werden. H2 wird vollständig im Prozess rezykliert und dient als Einsatzstoff bei der Methanisierung. Die Einzelschritte sind von den Verbundpartnern Karlsruher Flüssigmetalllabor (KALLA) am KIT, Climeworks Deutschland GmbH und INERATEC GmbH entwickelt, jedoch müssen weitere grundlegende Fragestellungen zur Systemintegration der Reaktorkomponenten und zur Skalierung mit Blick auf die CO2-Zerlegung gelöst und der Nachweis des komplexen Zusammenspiels erbracht werden. Die Kopplung der Prozessschritte ist bisher weltweit einzigartig und höchst anspruchsvoll. Ebenfalls Thema ist die Verwertung des Kohlenstoffs. Hierzu ist die systematische Charakterisierung produzierbarer Kohlenstoffpartikel notwendig, auf die aufbauend dann gezielt Verwertungswege definiert werden können.
Abb. 1: Schema der Verfahrensidee
Mit diesem Vorhaben entsteht ein innovativer Beitrag zum Erreichen der ambitionierten klimapolitischen Ziele weltweit, indem durch eine neuartige technische Lösung atmosphärisches CO2 als Quelle für den Wertstoff Carbon Black genutzt und damit zugleich zukunftsweisende, nachhaltige Geschäftsfelder geschaffen werden. Beides stärkt den Technologiestandort Deutschland.
With the Paris Climate Agreement of 2015, the international community committed itself to limiting global warming to below two degrees Celsius by the end of the century. In order to achieve this goal, global efforts to reduce greenhouse gas emissions will need to be accompanied by solutions to remove CO2 already emitted from the atmosphere. The overall objective of this project is the realization of a novel process to create "negative emissions" by decomposing atmospheric carbon dioxide into elementary, very pure carbon black and oxygen. A demonstration plant will be designed, built and operated over a longer period of time. In the planned process (see figure 1), CO2 is filtered out from ambient air by adsorption and will be converted into methane and water with hydrogen in a microstructured reactor. In further process steps, the CH4 is pyrolyzed in a liquid metal bubble column reactor, i.e. decomposed into H2 and C, and the H2O is split into O2 and H2 by solar powered electrolysis, which is not realized in NECOC, however. The carbon accumulates in the form of microgranular powder and can be used economically, for example, in the construction, rubber or electronics industries. H2 is completely recycled in the process and serves as a feedstock for methanization. The individual steps have in principle been developed by the partners Karlsruhe Liquid Metals Laboratory (KALLA) at KIT, Climeworks Deutschland GmbH and INERATEC GmbH. However, further fundamental questions regarding system integration of the reactor components and scaling with a view to CO2 decomposition must be solved and proof of the complex interaction must be provided. The coupling of the process steps is unique and highly demanding. Another topic is the utilization of carbon. This requires the systematic characterization of the achievable carbon particles, which can then be used as a basis for defining specific recycling routes.
This project will make an innovative contribution to achieving the ambitious climate policy goals worldwide by using atmospheric CO2 as a source for the recyclable material carbon black through a novel technical solution and thus creating forward-looking, sustainable business fields at the same time. Both of these factors strengthen Germany's position as a technology location.
KIT
Am KALLA besteht langjährige und umfangreiche Erfahrung in der Forschung zu Flüssigmetallen, wie z.B. Blei-Wismut, Zinn oder Natrium als Wärmetransportmedien (Homepage KALLA). Die Versuche reichen von grundlegenden generischen Experimenten bis zu Tests im Prototypenmaßstab. Die experimentelle Arbeit wird von theoretischen und numerischen Untersuchungen sowie Arbeiten zur Weiterentwicklung flüssigmetallspezifischer numerischer und analytischer Modelle zum Wärme- und Stofftransport komplementiert. Neben den eigentlichen Experimenten wird zudem die Entwicklung spezieller, flüssigmetallgeeigneter Mess- und Anlagentechnik vorangetrieben.
Das Herzstück des in diesem Vorhaben geplanten Prozesses ist die Methanpyrolyse, die am KALLA, u.a. in enger Zusammenarbeit mit dem Institut für Advanced Sustainability Studies IASS in Potsdam, in den vergangenen Jahren wissenschaftlich intensiv untersucht wurde. Die Arbeiten und Ergebnisse sind in mehreren Publikationen in wissenschaftlichen Fachzeitschriften [Gei15, Gei16, Ple15] und zwei Dissertationen [Ple17, Gei17] detailliert beschrieben. Abb. 2 links zeigt ein Verfahrensfließbild des am KALLA entwickelten und im Labormaßstab betriebenen Reaktorsystems. Aus einem Vorratstank wird reines Methan in einen mit flüssigem Zinn befüllten senkrecht stehenden Reaktor (Gesamtlänge von 1268 mm und Innendurchmesser von 40,6 mm, vgl. Abb. 2 rechts) über eine Einzeldüse (Austrittsöffnung mit Ø = 0,5 mm) eingeleitet. Die gebildeten Gasblasen steigen im Reaktor auf. Um eine gute Quervermischung sowie eine ausreichend lange Verweilzeit des Gases im Reaktor zu erreichen, wurde in die Flüssigmetallsäule eine Schüttung aus Glasringen eingebracht. Der Reaktor ist zur externen Beheizung in einem Ofen platziert und besteht aufgrund der korrosiven Eigenschaften des flüssigen Metalls aus einem Quarzglasrohr, das wiederum aus Stabilitätsgründen in ein Stützrohr aus Edelstahl eingebracht ist. Zur Bestimmung des Temperaturprofils in Strömungsrichtung sind im Inneren des Reaktors zahlreiche Temperatursensoren installiert. In den durch das umgebende heiße Metall erhitzten Gasblasen findet eine Zersetzung des Methans in gasförmigen Wasserstoff und festen, elementaren Kohlenstoff statt. Aufgrund des Dichteunterschieds zwischen Zinn und Kohlenstoff schwimmt letzterer oben auf und kann in Pulverform (vgl. Abb. 3 links) aus dem Reaktor an dessen oberem Ende bspw. gasgetragen abgeführt werden. Gegenüber herkömmlichen Rohrreaktoren verhindert die Verwendung des heißen Flüssigmetalls die Anlagerung dicker Kohlenstoffschichten an der Rohrwand, die zum Verblocken des Rohres führen würden. Dadurch wird ein kontinuierlicher Betrieb sowie die Herstellung des Kohlenstoffs in einer leicht transportablen und weiter verwertbaren Form ermöglicht. In einem dem Reaktor nachgelagerten Trennapparat wird schließlich der erzeugte Wasserstoff vom nicht umgesetzten Methan und teilweise auftretenden Begleitkomponenten zur weiteren Nutzung abgetrennt. Das restliche Gas wird dem Pyrolysereaktor erneut zugeführt.
Abb. 2: links: Fließbild des Methanpyrolyse-Prozesses zur Erzeugung von Wassersoff und Kohlenstoff; rechts: Detailansicht des mit flüssigem Zinn gefüllten Reaktors
Experimentelle Voruntersuchungen wurden in zweierlei Hinsicht ausgewertet. Zum einen wurde die Vollständigkeit der Reaktion anhand der Wasserstoffausbeute bei verschiedenen Prozessbedingungen bewertet und zum anderen wurden erste Analysen zum Kohlenstoff und seiner Beschaffenheit durchgeführt. Die experimentellen Arbeiten wurden durch umfangreiche theoretische Analysen begleitet. Außerdem wurden thermochemische und thermofluiddynamische Modelle entwickelt und miteinander gekoppelt, um die Vorgänge im Reaktor besser verstehen und wissenschaftlich fundiert beschreiben zu können.
Abb. 3: links: pulverförmiger Kohlenstoff (und Schüttungsringe aus dem Gasraum über dem Flüssigmetall) nach Öffnung des Reaktors im Anschluss an einen Versuch; rechts: Wasserstoffausbeute bei verschiedenen Feedvolumenströmen des Methans unter Variation der Reaktortemperatur zwischen 930 °C und 1175 °C
In Abb. 3 rechts ist die Wasserstoffausbeute in Abhängigkeit des Feedvolumenstroms an Methan und der Betriebstemperatur des Reaktors gezeigt. Es zeigt sich eine signifikante Abhängigkeit der Wasserstoffausbeute von der Reaktortemperatur, während der Methanvolumenstrom nur einen geringfügigen Einfluss auf den Umsatz hat. Mit steigender Reaktor- bzw. Flüssigmetalltemperatur nimmt die Wasserstoffausbeute erheblich zu und nähert sich zunehmend dem thermodynamischen Gleichgewicht an. Im Maximum konnte mit der verwendeten Versuchsapparatur eine Wasserstoffausbeute von knapp 80 % erreicht werden. Die Gasanalyse im Anschluss an den Reaktor hat gezeigt, dass als Nebenprodukte am Ende des Reaktors Ethan mit einer Konzentration von maximal 0,5 mol-% und Ethylen mit 1 mol-% nur in sehr geringen Mengen vorliegen. Mit dem passenden Reaktorkonzept und einer geeigneten Prozessführung können damit hohe Selektivitäten hinsichtlich reinen Wasserstoffs und elementaren Kohlenstoffs erreicht werden.
Mit Hilfe eines Rasterelektronenmikroskops wurde die Struktur des erzeugten Kohlenstoffs aus Probenentnahmen an verschiedenen Orten des Reaktors untersucht. Der im Produktgas mitgetragene Kohlenstoff im Filter nach dem Reaktor zeigt eine unstrukturierte Oberfläche mit Partikelgrößen im Bereich 2,5 – 9,5 µm. Der im Gasraum über der Flüssigmetalloberfläche des Reaktors abgelagerte Kohlenstoff ist plättchenförmig mit scharfen Ecken und weist Partikelgrößen im Bereich 4,5 - 24 μm auf. Im Gegensatz dazu zeigen die Kohlenstoffpartikel an der Reaktorwand Kugelform und haben eine Partikelgröße im Bereich 16 – 76 µm. Mit Hilfe der BET-Methode wurde zusätzlich die spezifische Oberfläche des Kohlenstoffs bestimmt, um auf dessen katalytische Aktivität schließen zu können. Da die spezifische Oberfläche des Kohlenstoffs lediglich im Bereich 8 - 23 m2/g liegt, wird davon ausgegangen, dass der in den Experimenten erzeugte Kohlenstoff einen vernachlässigbaren katalytischen Effekt auf die Reaktion hat [Ple17, Gei17]. Neben den Arbeiten von Serban et al. [Ser03] sind keine weiteren gleichartigen Untersuchungen aus der Literatur bekannt. Systematische Untersuchungen zur Abhängigkeit der Kohlenstoffeigenschaften von der Prozessführung wurden bisher weder von den Antragstellern noch anderen Gruppen durchgeführt und werden daher elementarer Bestandteil des hier geförderten Projekts.
Kontakte
Prof. Dr.-Ing. Thomas Wetzel, +49 721 608 46447 und 23462, thomas.wetzel∂kit.edu
Dr.-Ing. Leonid Stoppel, +49 721 608 26631, leonid.stoppel∂kit.edu
Dr.-Ing. Benjamin Dietrich, +49 721 608 46830, benjamin.dietrich∂kit.edu
M. Sc. Neele Uhlenbruck, +49 721 608 23446, neele.uhlenbruck∂kit.edu
Climeworks
Climeworks entwickelt und baut Anlagen, welche CO2 mit der weltweit ersten kommerziellen Direct Air Capture (DAC) - Technologie effizient aus der Umgebungsluft filtern. Die CO2 Filterung basiert auf einem zyklischen Adsorptions- /Desorptionsprozess mit einem strukturierten Adsorbermaterial, so dass der Energiebedarf für die CO2-Filterung aus der Luft minimiert wird (vgl. Abb. 4). Im ersten Schritt wird atmosphärisches CO2 (und H2O) auf einem festen Substrat adsorbiert. Im zweiten Schritt wird dann durch Erwärmung des Substrats auf ca. 100 °C das adsorbierte CO2 (und H2O) wieder desorbiert. Das desorbierte CO2 wird anschließend als reines Gas zur Verfügung gestellt. Das reine CO2 wird an Kunden in Schlüsselmärkten verkauft – beispielsweise die kommerzielle Landwirtschaft, die Lebensmittel- und Getränke-Branche, den Energiesektor und die Automobil-Industrie. Die DAC-Technologie kann in Verbindung mit CO2-Speicherung zur Produktion negativer Emissionen verwendet werden, die für die Erreichung der internationalen Klimaziele notwendig sind. Im Vergleich zu anderen sogenannten "Carbon Dioxide Removal" Ansätzen ist die DAC-Technologie unabhängig von landwirtschaftlichen Flächen, hat einen kleinen Fußabdruck und ist ohne Einschränkungen skalierbar. Messungen haben gezeigt, dass das so gewonnene CO2 eine Reinheit von 99.9+% v/v aufweist [Geb11, Geb13, Geb14, Wur11, Wur12].
Abb. 4: Prinzipdarstellung des zyklischen Adsorbtions- / Desorbtionsprozess der Climeworks-DAC-Technologie
Im Jahr 2017 hat Climeworks die weltweit erste DAC-Anlage auf kommerziellem Maßstab (900 Tonnen CO2 pro Jahr) in Betrieb genommen, mit welcher ein Gewächshaus in der Nähe von Zürich mit CO2 zur Düngung der Pflanzen beliefert wird (Abb. 5).
Abb. 5: Foto der weltweit ersten DAC-Anlage auf kommerziellem Maßstab
Im Oktober desselben Jahres hat Climeworks eine weitere DAC-Anlage in der Nähe von Reykjavik, Island in Betrieb genommen, mit welcher in Zusammenarbeit mit dem CarbFix-Projekt (vgl. https://www.carbfix.com/) erstmals atmosphärisches CO2 (50 Tonnen CO2 pro Jahr) dauerhaft und irreversibel im Boden versteinert wird (Abb. 6).
Abb. 6: Prinzipdarstellung des CarbFix Projekts
Kontakte
Dr.-Ing. Dirk Nuber, +49 221 29201060, dirk.nuber∂climeworks.com
INERATEC
INERATEC hat sich auf die Herstellung von mikrostrukturierten Reaktoren und modularen Anlagen für deren Einsatz spezialisiert, welche Gase wie CO2 und H2 in Kohlenwasserstoffe umwandeln können. Hierzu gehören neben Wassergas-Shift- und Fischer-Tropsch-Reaktoren auch solche für die Methanisierung. Die chemischen Methanisierungsreaktoren von INERATEC sind im Gegensatz zu zuvor beschriebenen, herkömmlichen Anlagen im Inneren mikrostrukturiert und mit einer innovativen Verdampfungskühlung ausgestattet (siehe Abb. 7) [Dit17, Bel17]. Durch eine Kühlung mit Siedewasser bei einem Druck von 5 - 20 bar bzw. 150 - 210 °C Eintrittstemperatur konnte ein gezieltes Austarieren zwischen hoher Wärmeübertragungsleistung und deutlich reduzierter Gefahr des Erstickens der Reaktion durch zu hohe Kühlflächenbelastung realisiert werden. Dadurch können in kompakten Reaktoren hohe CO2-Konversionsraten erreicht werden. Gleichzeitig kann die Reaktion temperaturkontrolliert mit dem Kühlmedium Wasser durchgeführt werden. Aufgrund der besseren Temperaturkontrolle werden längere Katalysatorstandzeiten erreicht und potentielles thermisches Sintern der Katalysatorpartikel bei hoher Temperatur wird vermieden. Industriell gezeigt werden konnte diese Technologie in dem europäischen Projekt COSIN (siehe Abb. 8) [Gui18].
Abb. 7: Methanisierungsreaktor der Firma INERATEC, hergestellt in Kooperation mit dem KIT [Dit17]
Das Reaktormaterial ist für minimale unerwünschte Kohlenstoffbildung im Reaktor ausgelegt. Großindustriell verfügbarer Katalysator wird als Festbett in den Reaktor eingebracht und kann bei Bedarf gewechselt werden. Bereits realisierte Module sind in der Lage, bis zu 2 Nm³/h Feedgas in 0,5 Nm³/h Methanprodukt umzuwandeln [Bel17, Pfe17]. Im Augenblick werden Module für 10 Nm³/h Methanproduktion gefertigt. Dies entspricht etwa einem maximalen Input von 40 Nm³/h Feedgas. Eine nächste Skalierungsstufe für die großtechnische Anwendung ist in Planung. Dabei lag bisher der Fokus der Produktion auf einem in das Erdgasnetz einspeisefähigen Methan als Endprodukt des Prozesses, d.h. der Minimierung von CO2 sowie der Optimierung des Brennwerts und des Wobbe-Index des Produktgases. Durch die Anpassungsfähigkeit des vorliegenden Reaktorkonzeptes, beispielsweise bezüglich Feedgaszusammensetzung und ein- bzw. zweistufiger Verschaltung von Reaktormodulen, können die vorhandenen Anlagen leicht an andere Prozessbedürfnisse angepasst werden. Dies soll nun demonstriert werden.
Abb. 8: INERATEC-Anlage aus dem europäischen Projekt COSIN
Kontakte
Dr.-Ing. Tim Böltken, +49 721 864844 63, tim.boeltken∂ineratec.de
Im Text verwiesene Publikationen:
[Bel17] | Belimov, M.; Metzger, D.; Pfeifer, P.: AIChE J. 63 (1), 2017, 120–129. |
[Dit17] | Dittmeyer, R.; Boeltken, T.; Piermartini, P.; Selinsek, M.; Loewert, M.; Dallmann, F.; Kreuder, H.; Cholewa, M.; Wunsch, A.; Belimov, M.; Farsi, S.; Pfeifer, P.: Current Opinion in Chemical Engineering 17, 2017, 108-125. |
[Geb11] | Gebald, Ch.; Wurzbacher, J.; Tingaut, P.; Zimmermann, T.; Steinfeld, A: Env. Sci. Technol. 45 (20), 2011, 9101–9108. |
[Geb13] | Gebald, Ch.; Wurzbacher, J.; Tingaut, P.; Steinfeld, A.: Env. Sci. Technol. 47 (17), 2013, 10063–10070. |
[Geb14] | Gebald, Ch.; Wurzbacher, J.; Borgschulte, A.; Zimmermann, T.; Steinfeld, A.: Env. Sci. Technol. 48 (4), 2014, 2497–2504. |
[Gei17] | Geißler, T.: Dissertation, KIT 2017. |
[Gei15] | Geißler, T.; Plevan, M.; Abánades, A.; Heinzel, A.; Mehravaran, K.; Rathnam, R.; Rubbia, C.; Salmieri, D.; Stoppel, L.; Stückrad, S.; Weisenburger, A.; Wenninger, H; Wetzel, Th.: Int J Hydrogen Energy 40 (41), 2015, 14134–14146. |
[Gei16] | Geißler, T.; Abánades, A.; Heinzel, A.; Mehravaran, K.; Müller, G.; Rathnam, R.; Rubbia, C.; Salmieri, D.; Stoppel, L.; Stückrad, S.; Weisenburger, A.; Wenninger, H; Wetzel, Th.: Chem. Eng. J. 299, 2016, 192–200. |
[Gui18] | Guilera J.: The COSIN project: synthetic natural gas production from biogas in a waste water treatment plant in Barcelona; ICREN 2018, 25-27 April 2018, Barceolona. |
[Pfe17] | Pfeifer, P., Belimov, M.: PCT/EP2017/063778, Patent, 2017. |
[Ple15] | Plevan, M.; Geißler, T.; Abánades, A.; Mehravaran, K.; Rathnam, R.; Rubbia, C.; Salmieri, D.; Stoppel, L. Stückrad, S.; Wetzel, Th.: Int J Hydrogen Energy 40 (25), 2015, 8020–8033. |
[Ple17] | Plevan, M.: Dissertation, KIT, 2017. |
[Sto17] | Stoppel, L.; Fehling, T.; Geißler, T.; Baake, E.; Wetzel, Th.: IOP Conf. Ser.: Mater. Sci. Eng. 228, 2017, 012016 |
[Wur11] | Wurzbacher, J.; Gebald, Ch.; Steinfeld, A.: Energy Environ. Sci. 4 (9), 2011, 3584–3592. |
[Wur12] | Wurzbacher, J.; Gebald, Ch.; Piatkowski, N.; Steinfeld, A.: Environ. Sci. Technol. 46 (16), 2012, 9191–9198. |